Kaizen Leader
Adopting a Kaizen mindset not only improves individual processes but also strengthens an organization’s ability to respond to change and develop its operations over the long term. The implementation of Kaizen requires a collective contribution and commitment from the organization to the improvement process.
Kaizen training is designed to support participants in implementing real development projects, ensuring that the lessons learned can be directly applied in the work environment. With the emphasis on how to organize a successful Kaizen event, the training pays particular attention to the importance of collaboration and communication. You will also learn about change management, enabling you to prioritize solutions and develop an implementation plan that will move the organization toward the target state.
Please note that this program is held in Finnish.
What is Kaizen?
Kaizen is a Japanese term meaning "change for the better." It focuses on continuous improvement at all organizational levels, with the aim of gradually improving processes, products, and services, leading to significant long-term improvements. The benefits of Kaizen are manifold: it increases productivity, improves quality, engages employees, and delivers cost savings. However, its implementation can face challenges such as resistance to change, time and resource requirements, and lack of management commitment. The success of Kaizen, therefore, requires the collective commitment of the whole organization and continuous engagement in the improvement process.
Benefits
The training program provides practical tools and methods to help you improve the efficiency and smooth running of your business. You will learn how to identify process bottlenecks and eliminate waste through Lean thinking. It provides clear steps to support continuous improvement.



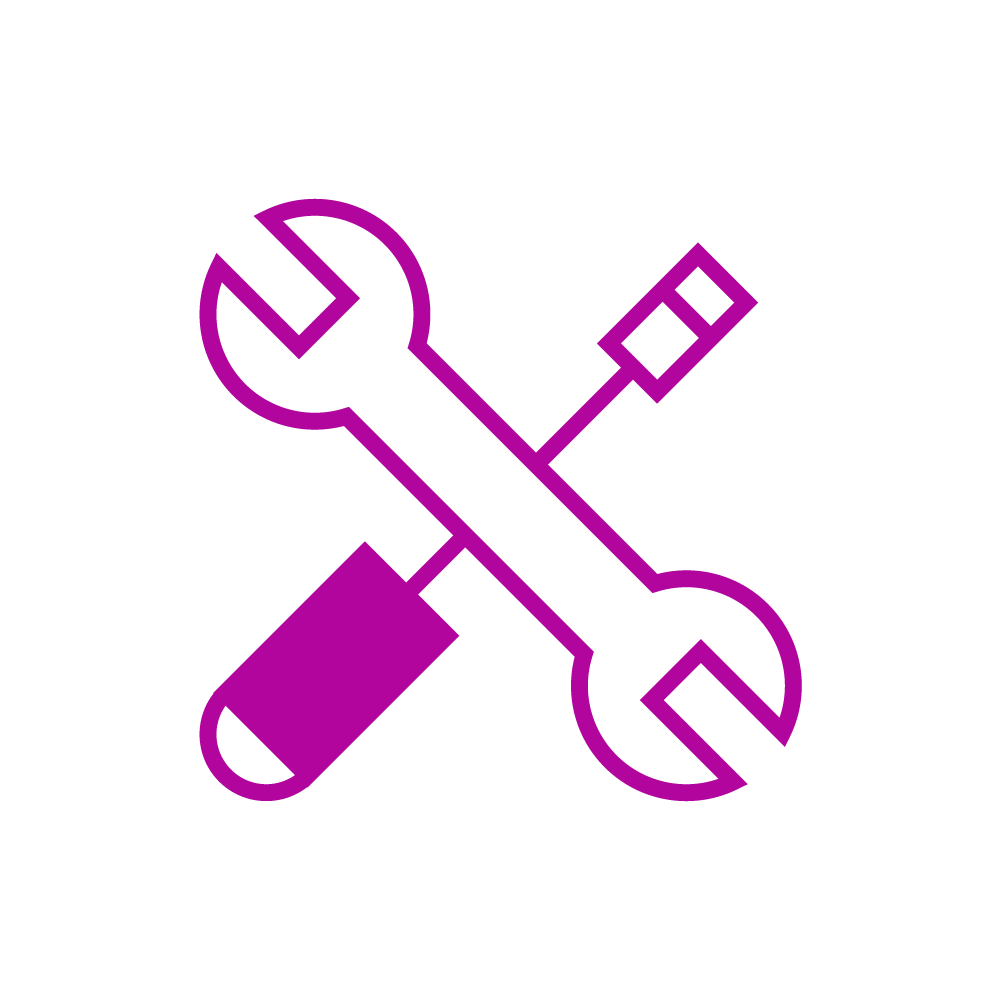
For
Kaizen training is particularly suitable for people who are responsible for development projects and process improvement in their organization or team. It is suitable for process managers, team leaders, development managers, and specialists who want to deepen their understanding of Lean methods and learn practical tools to support continuous improvement.
Contents and Schedule
The training days will consist of instructor-led lectures, group work, and exercises. Day 1 will focus on the basics of Lean thinking, Kaizen methodology, and current state analysis through value stream mapping and root cause analysis. Day 2 will focus on defining the goal state process, prioritizing change and planning, and implementing and measuring development activities.